The Owl® 4 is a patented, non-contact optical system measuring the glass thickness, type of low-E coating (1, 2, 3 silver layers, 4th surface low-E), glass dimensions and sheet locations as the load approaches the furnace.
The Owl® 4 transmits data to the furnace control system allowing the furnace to automatically select a recipe and optimize the heat profile, improving cycle time, minimizing distortion, and optimize flatness. The Owl® has a proven track record of improving productivity and quality in glass manufacturing plants since 2002.
The addition of the Load Validator™ system to the Owl® 4 detects fault conditions in the glass or load geometry and alarms the conveyor system to stop the glass load before the load enters the furnace, thereby eliminating several sources of glass breakage and subsequent interruption to the tempering system. Faults Detected include wide load, part overlap or stacking, vent or short crack, broken glass, short part, minimum distance between parts, corner off, and long load.
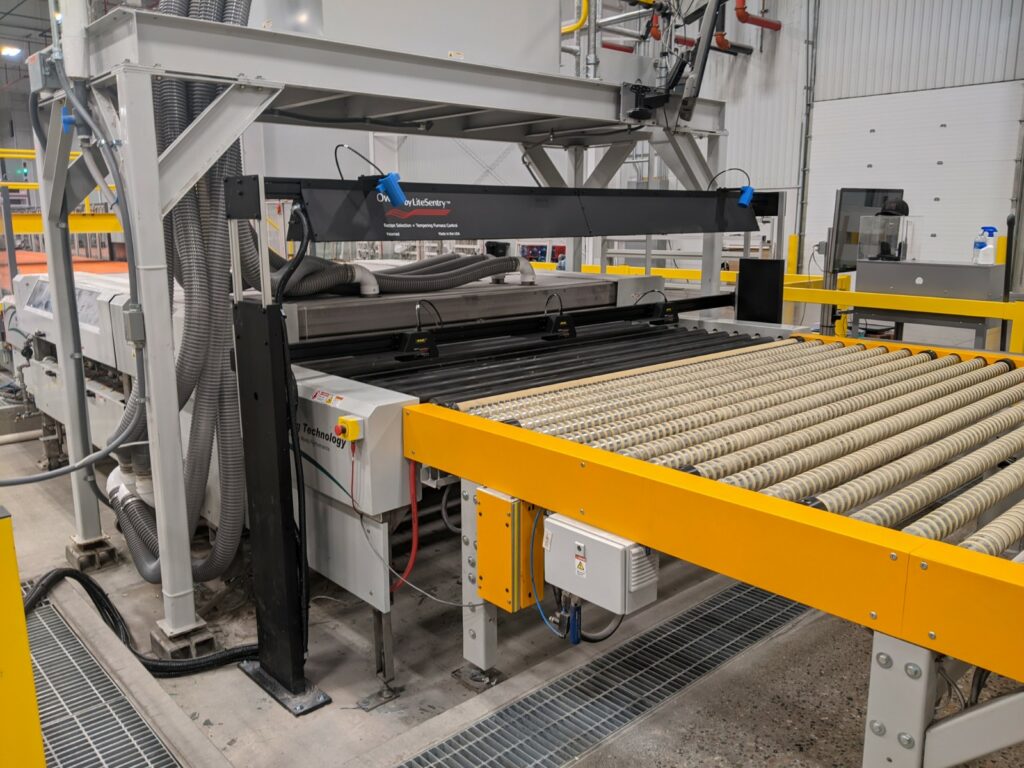
- Non-contact, real-time measurement of glass size, thickness and low-E coating
- Automatic furnace control selects recipe and heat time or heat profile
- Temper QC outputs to furnace include:
- Area and location of each glass sheet
- Thickness and coating type
- Bed yield or percent bed utilization
- Optimized heat time/profile saves seconds on every load = multiple extra loads everyday
- Improves optical quality by optimizing heat-time or heat-profile and preventing overheating of small loads
- Eliminates lost production due to recipe changes
- Eliminates operator errors due to incorrect inputs
- Ability to stop a faulty load from moving into the furnace.